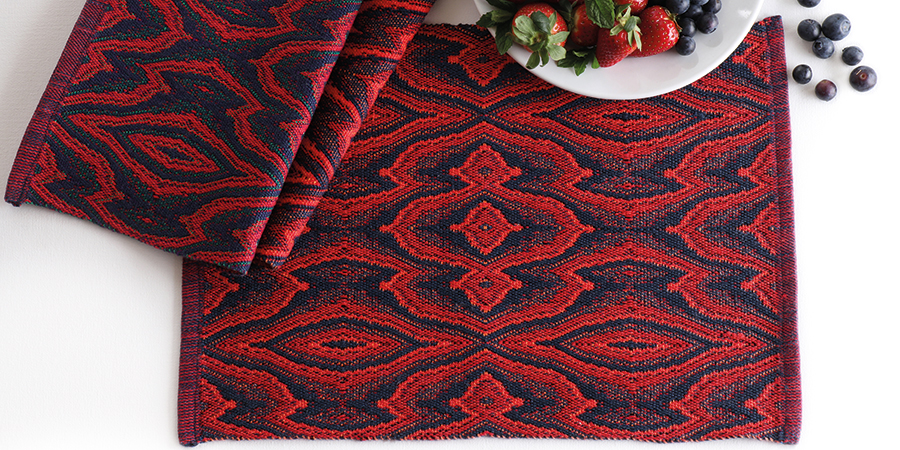
Four colour double weave
Agnes Hauptli is an award-winning member of the Professional Weavers Network of New Zealand. Agnes loves her 16 shaft Ashford table loom and with these four colour double weave placemats, she really shows its capabilities!
Happy weaving!
You need a 16 shaft loom especially if you like more complex designs. If you like patterns with curves and circles you can get a much smoother design line on more shafts. Advancing twill lines have a much bigger design area on sixteen shafts than it would on eight. If you love turned twill blocks and want four blocks, you’ll need sixteen shafts. If you love Echo weave designs, turned Taquete, or interleaved designs, then a 16 shaft loom is what you want.
Start designing your own patterns, get really comfortable with a specific structure in weaving. That could be summer and winter, lace weaves, crackle, twill, network twills and many others. Use today’s modern tools in the form of weaving software such as PCW Fiberworks, WeavePoint, ProWeave or WeaveIt. Play with that structure, expand the threading, change treadlings, play around with the tie-up. You will soon see that designing takes up more time than the actual weaving and it’s a lot of fun too!
I also like to have the 16 shaft table loom for sampling. If I just quickly want to see if a specific structure or design will work, it is much more economical to set up the table loom than a floor loom.
Another huge plus for the table loom is the ability to lift each shaft individually in any way and in any combinations you want. My nickname for it: it’s the manual dobby loom. Sometimes, on a 16 shaft floor loom with treadles one can be limited with lifts because of the tie-up. Yes, there is skeleton tie-up options but it’s just not so practical if one has to press down three treadles.
Go on push the limits… with a 16 shaft table loom! ~ Agnes
Agnes weaves these four colour double weave placemats, she really shows the capabilities of her 16 shaft Ashford table loom!
For this project I decided to do placemats using an 8/2 Ne mercerised cotton in a four colour double weave.
You will need:
Loom: 16 shaft table loom 60cm (24ins) wide
Reed: 48/10cm (12dpi)
Sett: 19epcm (48epi)
Warp yarn: 8/2 Ne mercerised cotton, 6700m/kg in two contrasting colours of similar value. I used red and navy, 1 cone each
Weft yarn: 8/2 Ne mercerised cotton, 6700m/kg bright green and medium blue, 1 cone each
Here’s how:
Number of ends: 573 ends, alternating red and navy
Width in reed: 30.5cm (12ins)
Finished size: 27cm (10½ins)
Warp length for four placemats: 1.8m (6ft) plus loom waste and sampling
Weave structure: Four colour double weave
Weaving
Weave 3cm (1¼ins) in plain weave using a finer cotton for hem. Weave according to the draft for the required length alternating your weft colours.
Finishing
Fold hem and machine stitch. Wash in washing machine on full cycle, iron.
Four Colour Double Weave
In classic double weave we usually have two colours in the warp and the same two colours in the weft and therefore create areas of pure colour. In four colour double weave two different colours are used in the weft which creates areas of four combinations of mixed colours and no areas of pure colour as in the following drawdown:
Depending on the thickness of yarns used, this structure can be used for a variety of items. If using thicker yarns like 8/2 Ne cotton this makes sturdy placemats, table runners, bags or jacket material. If you use finer yarns like 30/2 or 60/2 Nm silks, gorgeous scarves and shawls can be produced. With the right placement of colours, a certain amount of iridescence can be achieved.
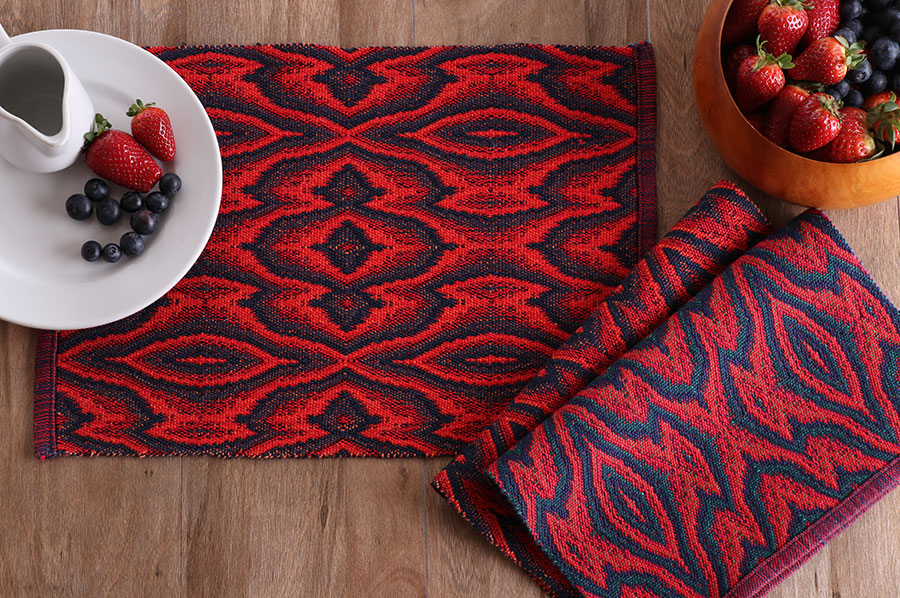
Textiles have always played a part in my life. When I was very young my grandmother taught me how to knit. Later I was fascinated with very fine crochet work, and embroidery took my fancy for a while. As kids, living in a time with no TV or other electronic time-wasting gadgets, we were steered into making presents instead of going into a shop and buying something. The seed was sown.
In 1995 whilst on a visit in Switzerland I was given a rigid heddle loom. Back home I gave it a go, was fascinated and couldn’t stop playing with my new toy! Over the next several years there was a steady progression from loom to loom: I had to build a separate building to house all these looms! Today my workshop houses 5 big looms, a couple of smaller floor looms and in a separate room there are several table looms, amongst them two 8 shaft and a 16 shaft loom which are used for sampling and for teaching. The beauty of these is that you can attach a second warp beam for weaves where you are using two warps with differential take-up.
With the change of looms the threads changed as well. While I was using rough carpet wool on my very first trials on the rigid heddle loom, with each new loom acquisition I also seem to have changed the threads and very quickly ended up with very fine silks as my absolute favourite. To thread my 32 shaft loom with 90-120epi does not put me off at all – on the contrary!
I am fascinated by the absolutely endless possibilities in view of design and I also marvel at the different materials we have today. From drinking straws to copper wire to flower stalks to aluminium strips, anything goes. But besides the different materials one can use, it is the design aspect and the choice of colours that attracts me the most. Thanks to weaving software that is readily available today we can explore weave designs like never before.