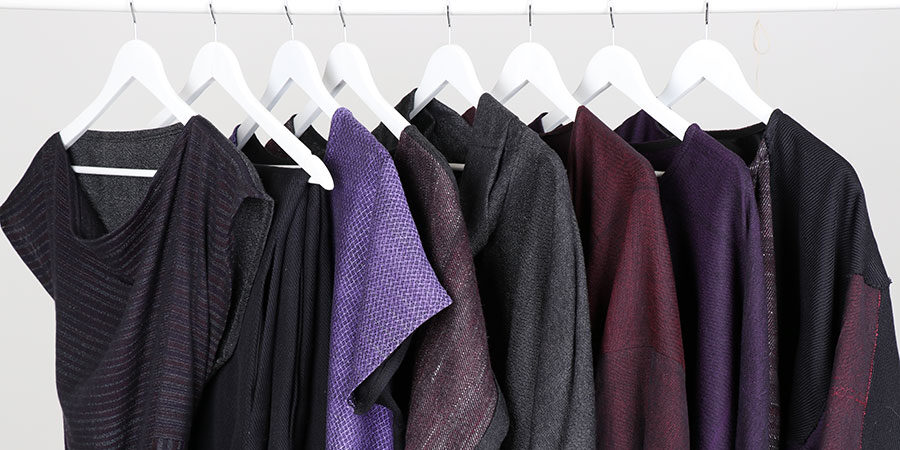
One warp, one wardrobe
The long story of a long warp. One warp one wardrobe was an idea that I came up with to challenge myself and my loom. If you know me, you probably know that sometimes I just “wing it” rather than working out the full plan before I start something – the ideas sometimes evolve as I go. This particular project didn’t veer too much in the overall plan – placing one warp on my loom to weave fabric for a capsule “one” wardrobe, however the details did change and evolve along the way.
I hope you enjoy reading about this project and I would love to hear from you about your weaving to wear projects or if you have any questions about my project email kate @ ashford.co.nz (without spaces).
The plan:
To weave fabric, to sew into clothing that would co-ordinate and work together to create a capsule wardrobe.
My first thoughts were what yarn to use as the warp – I needed something that would be versatile and work with lots of other yarns so of course I chose black as the colour. I wanted a finished fabric that would be a nice weight for clothing. I narrowed it down to 10/2 cotton and then only had to decide if I wanted to use the mercerised or unmercerised, I went with the shiny mercerised 10/2.
I did not calculate how much warp length I would need – I decided on 30m and would use the fabric to make as many garments as I could. I ended up only using 26m as time was running out.
Loom: Ashford Jack loom
Warp yarn: Ashford 10/2 Mercerised Cotton
Warp length: 30m (33yds)
Width in reed: 37″
Fabric finished width after waashing: 36″
Sett: 24epi – double sleyed in a 12dpi reed
Threading: Straight 1,2,3,4,5,6,7,8
You might be wondering how I wound a warp 30m long when my warping frame is only 11m? I added some extensions to my frame.
Initially I thought I would weave sections of fabric in different weave structures. However after weaving the first section of fabric I decided there was probably a reason that 80% of the woven fabric used in the world today is plain weave! and proceeded to weave most of the sections in plain weave and twill.
Did you know: Twill fabric is more durable and flexible than plain weave. The reason being the number of interlacements is less. (refer to my article “Let’s talk about Setts” from issue 30 of The Wheel magazine).
Fabric 1 The weaving began, first up was about 4m in twill, using the same yarn as my warp for the weft. This would be for my pants option – which ended up being a jumpsuit and is my favourite piece!
Fabric 2 Then I moved on to a section in twill with a handspun single as the weft. Ashford Silk/Merino blend spun into a fine single.
Fabric 3 The next section was a hand dyed silk weft. Ashford 20/2 Silk dyed with Ashford Protein Dyes – Violet. I played around with patterns but soon decided I preferred plain or twill!
Fabric 4 I switched back to plain weave but the pattern came from the yarn. I had a cone of very fine multi-coloured cashmere yarn which wove up beautifully and the way the yarn was dyed it came out with stripes on the fabric.
Fabric 5 Plain weave again with an unidentified grey marled wool cashmere blend as the weft – please don’t ask me what the yarns are – I have so many cones in my stash with no labels on.
Fabric 6 Plain weave again with a fine burgundy Tencel yarn as the weft – the drape on this fabric was beautiful!!
Fabric 7 Plain weave again with a fine purple cashmere silk blend as the weft.
Fabric 8 Plain weave with a fine black wool as the weft.
The process:
Once the weaving was complete, I removed the fabric from the loom and cut and overlocked (serged) the end of each section then washed each piece in the washing machine, line dried and then ironed. It is very important to finish the fabric BEFORE sewing.
Did I realise there was a sleying error (4 threads in one slot on the reed instead of two) yes I sure did! – after about 20cm of weaving – but I decided to leave it just to remind everyone it was hand woven fabric and not all fabric needs to be perfect….well that is not really true…I really left if because I was too lazy to stop and re-sley the reed!
Once my fabrics were all washed, dried and pressed I set to working out what garments I would make with which fabric – as each of the sections were different lengths. My general thoughts were – pants, skirt, tops, jacket. This evolved into a shift dress, a jumpsuit (with pockets!), 3 short sleeve tops and 1 long sleeve top and 2 jackets.
I don’t use sewing patterns – I usually find something that fits me and copy from that. I have included some rough outlines of the shapes. Again, if you know me you will know I am a bit lazy and find the simplest way I can do something – hence the simple shapes in my patterns.
★The unwinding★
Fabric 1 – JUMPSUIT
The pattern is cut out in 4 pieces, front left, front right, rear left and rear right. There are seams up each side and up the middle. I am a very rectangular shape so don’t need any darts or pleats – but I find that a little elastic across the back does work well on this pattern if you need shaping. I also added pockets – because pockets!
Fabric 2, 3 and 5 – SHORT SLEEVE TOPS
One of my favourite patterns – it is so simple and uses very little fabric as you can use the selvedge edge as the hem. I use bias tape on the neckline to make a nice finish. I used the plain black Fabric 8 as the back of both tops. I also made a loose cowl neck top from Fabric 5 – the same general shape as the short sleeve tops but with a large oversized cowl neckline.
Fabric 4 – SHIFT DRESS
I loved how this one turned out. I used Fabric 4 for the front of the dress and Fabric 5 for the back and the tie. The dress is a simple design. the front is a rectangle for the lower half and the top is an isosceles trapezoid shape – the extra width across the top gives the drapey cowl neckline. The back of the dress is a rectangle. It has splits on each side and a tie at the waist – which can be worn to the front or the back.
Fabric 6 – KIMONO JACKET
This is a super easy pattern and really does not use much fabric. Basically, a folded over rectangle, cut and shaped a little for the centre front then add large rectangular sleeves. There is no facing on the neckline, so I reinforced with some thin web tape just across the back of the neck.
Fabric 7 – LONG SLEEVE TOP
Again just the simple shape top as above but with long sleeves and a longer hemline.
All the scraps – BOG JACKET
I sewed the scraps of handwoven fabric onto a cotton fabric from my stash and made a bog jacket. (Google Bog Jacket pattern)
Did you know: The history of the Bog Jacket pattern is very cool – dating back to the bronze age! Zero waste sewing is certainly not a modern thing! Thank you Liz Haywood – for your diagram.
The outcome:
I ended up with a capsule wardrobe made up of eight garments that can be worn in many combinations!
I am really happy how this project turned out – making your own clothing from your own handwoven fabrics takes the satisfaction levels to an all new high!
★★★One wardrobe★★★